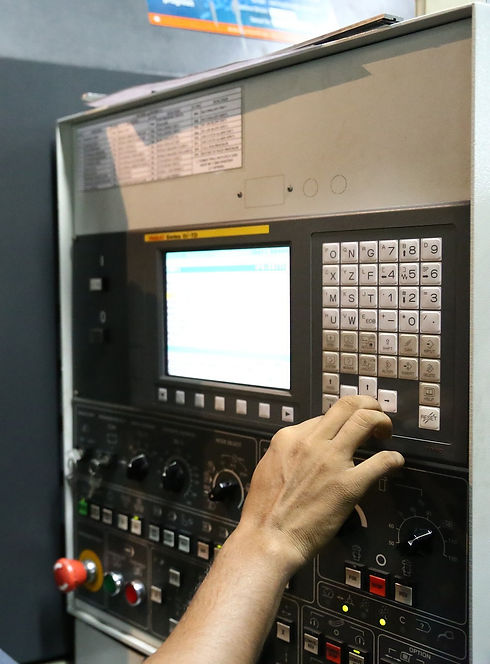
The Process
Injection moulding is a manufacturing technology for the high volume production of plastic parts.
It is a process where a material is heated to its melting point and then forced through an injection port to fill a formed cavity at high pressure. As the material cools, it will solidify into the shape of the cavity. The materials used in Injection Moulding are thermoplastic polymers that can be coloured or filled with other additives.
Injection moulding is so popular, because of the dramatically low cost per unit when manufacturing high volumes and is used for making complex car parts to basic kitchen appliances. Injection moulding offers high repeatability and good design flexibility.
The mould
The simplest way to define a mould is it’s like the negative of a photograph: its geometry and surface texture is directly transferred onto the injection moulded part.
A high level of expertise required to design and manufacture a high-quality mould that can produce thousands of parts accurately.
Moulds are usually CNC machined out of aluminium or hardened steel and then finished to the required standard. It usually makes up the largest portion of the start-up costs in injection moulding.
The cost of a typical mould starts as low as $5,000 for a simple geometry and relatively small production runs (1,000 to 10,000 units) and can go upwards to $100,000 for moulds optimized for full-scale production (100,000 units or more).
The design complexity also comes from the other features that are extremely critical; the runner system that facilitates the flow of the material into the mould, and internal water cooling channels that aid and speed up the cooling of the part.
video of the product to give your clients a way of visualizing what you are selling.
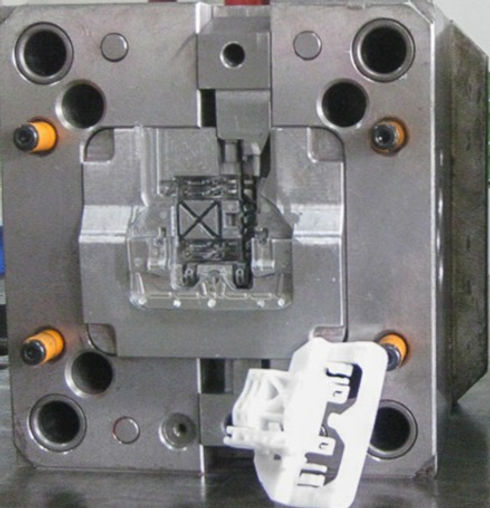

The anatomy
The simplest mould is the straight-pull mould. It consist of 2 halves: the cavity (the front side) and the core (the back side).
In most cases, straight-pull moulds are preferred, as they are simple to design and manufacture, keeping the total cost relatively low. There are some design restrictions though: the part must have a 2.D geometry on each side and no overhangs. If more complex geometries are required, then retractable side-action cores or other inserts are required.
Side-action cores are moving elements that enter the mould from the top or the bottom and are used to manufacture parts with overhangs (for example, a cavity or a hole). Side-actions should be used sparingly though, as the cost increases rapidly.
Design Tip: About 50% of the typical injection moulding cycle is dedicated to cooling and solidification. Minimizing the thickness of a design is key to speed up this step and minimise costs.